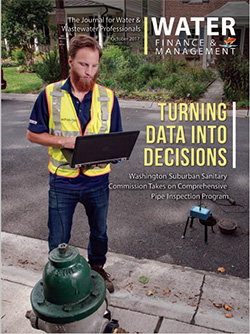
DOWNLOAD THE PDF
Water asset management can be a lofty enterprise, particularly if you’re one of the largest utilities in the United States. The Washington Suburban Sanitary Commission (WSSC), established in 1918, covers nearly 1,000 sq miles in Prince George’s and Montgomery counties in Maryland and serves 1.8 million residents through approximately 475,000 customer accounts. It operates three reservoirs that combine for a typical total holding capacity of 14 billion gal; two water filtration plants with the capacity to produce 390 mgd of safe drinking water; and six wastewater treatment plants with a total capacity to handle 95.62 mgd of wastewater.
The WSSC’s buried water infrastructure comprises more than 5,657 miles of water main lines and 5,687 miles of sewer pipeline. A sizeable portion of them, however, are likely to be more than 50 years old, according to Gary Gumm, Chief Engineer of the WSSC since November 2007. “Some of the water main pipes are up to 100 years old, and some we just put in recently. But almost half of what we have is probably over 50 years old,” he said. “And they’re needing to be replaced.”
Mapping Out Asset Management
In order to stay on course and maintain its level of service despite the aging infrastructure, the WSSC develops asset management plans of all water system elements that it owns and operates, from the buried pipes and sewer systems to the vertical (aboveground) dams, plants and buildings where employees work.
“We approached the comprehensive evaluation in different ‘chunks’ according to different areas of the organization,” said Fred Pfeifer, WSSC’s Asset Strategy Manager, who also manages capital maintenance cost projections for the utility’s water infrastructure. “The buried water lines were one of the earliest and largest ‘chunks’ we attempted, and that’s about over 150,000 pipe lengths. These can be fairly long, anywhere from 200 to over 1,000 ft.”
Traditional methods of identifying pipe for replacement include examining records of past breaks, reported leaks and water quality complaints from customers. The WSSC currently relies on the decay model for asset management (AM), which forecasts pipe conditions out to 30 years based on mathematical decay curves computed from variables such as asset type, maintenance and break history, construction year and fire flow results. Condition ratings are also assigned based on the pipe’s age, material, installation, work order history and inspection history. The calculated probability of failure, combined with the potential consequences of such a failure, is used to prioritize pipes for replacement.
While a reliable industry standard, the AM decay model can still be problematic when replacing water main lines for several reasons, according to Pfeifer. “Because it’s buried, you can’t see it for yourself, and unlike sewer pipe, you can’t go inside with a camera or robot so it’s largely been hypothetical,” he said. “The ages we have are based on original industry estimates, which can be unreliable. For example, a manufacturer in 1930 would say the pipe will last for 75 years without having anything to predicate that on, and nobody ever went back to determine if that 75 was right or wrong. If it was wrong, would it be shorter or longer?”
In 2011 the WSSC was introduced to acoustic-based technologies from Echologics that could non-invasively detect leaks and inspect pipe conditions. A non-intrusive, non-disruptive technology, Echologics’ ePulse® assesses water mains through the use of acoustic sensors. It collects data that, when averaged, indicates minimum wall thickness of pipe segments and checks for leaks throughout the water distribution system. To determine the viability of the condition assessment technology, the WSSC decided to launch a pilot study of pipe sections it had already earmarked for replacement.
“It could take decades to go around collecting individual pipe samples for lab testing whenever we would replace pipe,” Pfeifer said. “We had some that we were already planning to replace when we came across the technology, so we decided to test it and compare the acoustic results with the lab tests and see if the two lined up.”
Testing the New Technology
The pilot study conducted with Echologics focused on 32 cast iron pipeline segments at varying lengths, with an average of 200 ft each, all of which were already scheduled for replacement based on previous decay model predictions. Echologics was tasked with providing the remaining wall thickness using its acoustic-based technology, while the WSSC would be interpreting the pipe’s remaining life. At the request of the WSSC, Echologics also custom-engineered a scoring system that relates the pipe’s current progress from new pipe condition (1.0) to reaching its failure thickness (5.0) to conform to WSSC’s scoring system for all assets.
The pilot’s acoustic tests were conducted during construction in spring 2012 and showed that approximately 70% of the cast iron pipes still had sufficient levels of remaining wall thickness and thus were not in need of replacement; almost 40% of the segments were indicated to be at or near their original condition. To validate these results, the WSSC performed visual and ultrasonic testing at several sites to measure the thickness of the pipe. Soil samples and pipe coupons were also obtained for testing. It was found that while the field measurements correlated with the acoustic measurements taken by Echologics, neither matched up with the original AM decay model.
“Our model was way more aggressive than it should have been,” said Pfeifer. “We thought the pipe was in really terrible shape, yet both the acoustic and the lab indicated it really wasn’t. We thought that maybe about a third to half of the pipe was in much better condition than we estimated.”
Of the 32 pipe segments analyzed, the model predictions for 9 of them, or 22%, did not match with the data obtained from the field measurements. Pfeifer explained that there were likely initial errors in the data used, and after revising the AM decay model, he and the buried water asset manager set out in 2013 to perform a second field test. “We needed a bigger sample to make sure,” he said. “First we corrected a couple errors made in our protocol the first time, since it was kind of new for everybody. And in the second test, we got a pretty good correlation with the AM decay model and the larger sample.”
The Pipe Inspection Program
Following the pilot study and subsequent field test, Pfeifer said recommendations were made to include acoustic-based condition assessment in the WSSC’s programming. “The idea is to do 50 to 100 miles a year so that we could begin to build an inventory and get ahead of the pipes and have some degree of assurance that the prediction model is correct,” he said. “We can actually kind of bring that now into alignment.”
Part of a much larger vision the utility is putting together, condition assessment is now a valuable tool for the WSSC in finding out what’s going on in the pipe you can’t see. At the WSSC, future water main replacement projects are selected based on different “levels” of inspection. The first level—the AM decay model—is able to study 100% of the assets the utility owns but ultimately needs to be verified since it is purely hypothetical and is the least reliable method within the WSSC’s toolbox. Acoustic-based condition assessment now brings the utility to more easily inspect at the second level. Since it is more costly and logistically difficult to physically dig up all pipes for inspection (considered the highest level of the inspection program), the utility utilizes condition assessment to corroborate findings amongst its inspection protocols.
Complicating this is the variation in pipes and pipe repair procedures over the years. While most of the WSSC’s assets are made of cast iron, ductile iron is now the pipe of choice despite being thinner and typically more susceptible to corrosion, according to Gumm. To counteract this, they also developed a program to ward off corrosion, enabling them to place more of the new ductile iron pipes. Pfeifer said even their cast iron inventory varies, identifying at least four different versions with different properties, meaning they will “need to get about 300 to 400 good samples of each category in order to have a valid statistical sample. So that’s kind of what we’re working toward, and it will likely be a decade-long project.”
Pipe Replacement Goals
The ultimate goal is to ensure accurate and cost-efficient pipe replacement of the aging water infrastructure. “In 1989 we actually accomplished 1.7 miles of water mains reconstructed,” Gumm said. “Our target for the year this year is 61 miles, so it’s grown quite a bit in those decades.”
He added that as more pipes reach old age, more miles of reconstruction will be needed. “Knowing which 61 miles of pipe to replace is the challenge right now,” Gumm said. “It’s very important to have the technology to replace the right pipe.” “Our customers count on us to deliver safe, clean drinking water and make smart financial decisions with their money,” said WSSC General Manager and CEO Carla A. Reid. “Using technology to prioritize water main replacement enables us to fulfill our clean water mission and gives our customers a greater return on the money they’ve invested in our pipes.”
DOWNLOAD THE PDF